塑料发泡挤出机的高效生产需通过
设备优化、工艺参数精准控制、原材料适配及自动化管理等多维度协同实现,核心目标是在保证发泡制品质量(如泡孔均匀性、密度稳定性)的前提下,提升挤出速度、降低能耗并减少废料。以下是具体实现路径:
螺杆与机筒设计升级
高效螺杆构型:采用屏障型螺杆或分离型螺杆,通过设置混合段、剪切段的特殊螺棱结构,增强物料塑化均匀性(避免局部过热或未熔颗粒),同时减少熔体输送阻力。例如:在 PP 发泡挤出中,螺杆长径比(L/D)可提升至 30-40,确保熔体充分熔融并与发泡剂均匀混合。
机筒温控分区:采用多段式加热 / 冷却系统(如 3-5 个温控区),精确控制不同区段温度(如喂料段防粘、压缩段熔融、均化段稳定熔体黏度),避免因温度波动导致发泡剂分解不稳定。
发泡剂注入系统精准化
模具与定型系统优化
熔体黏度与压力控制
熔融压力稳定:通过螺杆转速与背压联动调节(如采用变频电机 + 压力闭环控制系统),使机筒末端熔体压力波动控制在 ±5bar 以内。例如:PVC 发泡挤出中,熔体压力过高会导致发泡剂提前逸出,过低则泡孔易塌陷,需维持在 150-200bar 的稳定区间。
熔体黏度匹配:根据原材料特性(如 HDPE 与 LDPE 的熔体流动速率 MFR 差异),调整螺杆转速(通常 100-300rpm)和机筒温度(如 PE 发泡温度 150-180℃,PS 发泡 170-200℃),确保熔体黏度与发泡剂溶解度适配(黏度过高则发泡剂分散困难,过低则泡孔易合并)。
发泡剂类型与用量适配
物理发泡剂高效利用:采用超临界流体发泡技术(如将 CO₂压缩至 7-10MPa 的超临界状态),其在熔体中的溶解度更高(是常规液态的 2-3 倍),可减少发泡剂用量并获得更细密的泡孔(直径≤0.1mm),同时降低因发泡剂泄漏导致的原料浪费。
化学发泡剂协同使用:在低发泡倍率(如 1.2-2 倍)制品中,可复配化学发泡剂(如 AC 发泡剂)与物理发泡剂,利用化学发泡剂的放热分解特性辅助熔体升温,减少机筒加热能耗,同时提升发泡稳定性。
冷却与牵引速度协同
原料干燥与杂质控制
配方优化(提升熔体强度)
添加成核剂:在 PP、PE 等结晶性塑料中加入滑石粉、碳酸钙等成核剂(添加量 0.5%-2%),增加泡孔成核点数量,使泡孔更细密(泡孔密度提升 30% 以上),同时增强熔体强度,避免发泡过程中泡孔合并。
弹性体改性:对于低熔体强度原料(如 LDPE),混入少量 EVA 或 POE 弹性体(5%-10%),提升熔体的拉伸黏度,防止泡孔在膨胀阶段破裂,允许更高的发泡倍率(从 2 倍提升至 5 倍以上),间接提高单位时间产量。
在线监测与闭环控制
实时参数监控:通过安装熔体压力传感器、红外测温仪、泡孔图像分析仪(如激光扫描检测泡孔直径分布),实时采集数据并反馈至 PLC 系统,自动调节螺杆转速、发泡剂注入量、牵引速度等参数(响应时间≤0.5 秒),避免人工调节滞后导致的质量波动。
能耗优化:采用变频电机驱动螺杆和牵引机,根据物料流量自动调节输出功率(如低负荷时降低转速,能耗可降低 15%-20%);同时通过余热回收系统(如将机筒散热用于原料预热),提升能源利用率。
快速换产与维护设计
塑料发泡挤出机的高效生产是 **“设备硬件升级 + 工艺参数精准化 + 原材料适配 + 智能化管控”** 的综合结果。通过优化螺杆塑化效率、提升发泡剂混合均匀性、强化定型冷却速度,并借助自动化系统实现实时调控,可在保证制品合格率(≥98%)的前提下,将挤出速度提升 20%-50%,同时降低单位能耗 10%-30%,最终实现高效、稳定、低成本的生产目标。
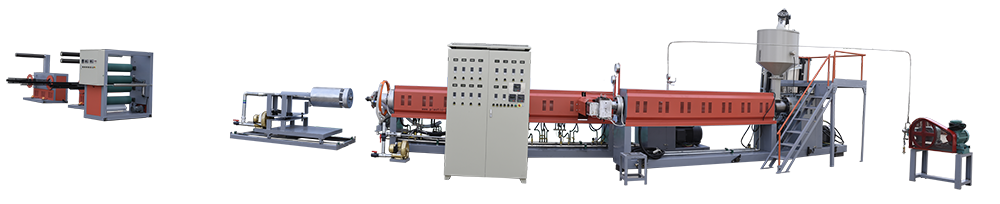